記事のポイント
- 化学メーカーのダイセルは20年前からDXで生産革新を実現する
- 2020年には「最適運転条件導入システム」と「高度予知予測システム」を開発
- 工場の働き方改革を実現し、今後はグループ、サプライチェーンに拡大予定だ
プラスチックを製造するプロセス型化学メーカーのダイセルは2000年度、先人が積み重ねた知見とテクノロジーを駆使し「ダイセル式生産革新手法・知的統合生産システム」を構築しました。生産技術やノウハウが属人化しやすいというプロセス型製造の、技能伝承や工場運営の標準化における課題を解決する為のシステムです。システムは2020年度「自律型生産システム」に進化し、サプライチェーン全体でのエネルギー最適化を目指し、今後はグループ企業、サプライチェーンに拡大の予定です。(オルタナ総研フェロー=室井孝之)
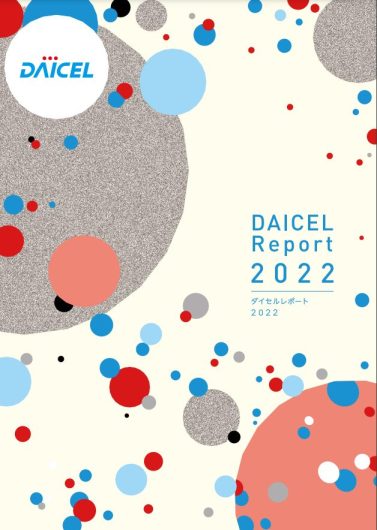
製造業では、2つのタイプの生産現場があります。自動車、家電製品、造船など組み立てと加工をメインとする組み立て型(アッセンブリー型)と、石油精製、鉄鋼、化学、半導体など連続して材料を流し製品化するプロセス型です。
プロセス型は、データを活用した高度な制御技術が欠かせません。
同社は1990年後半、世代交代におけるプラント運転技術の伝承の課題への直面を契機に、工場運営における改革を「人・組織」「生産システム」「情報システム」の3つの視点から進めました。
熟練オペレーターの暗黙知である運転に関する約840万件のノウハウを可視化し、その意思決定フローを運転支援システムに落とし込み、誰もが高品質に業務を行える体制を構築しました。
その結果、徹底的なムダの排除が出来、網干工場(兵庫県姫路市)では、生産性3倍、総原価20%削減を達成しました。
同社は、団塊世代の大量退職による生産性低下が懸念された「2007年問題」を前にシステムを確立し、大幅な生産性向上を実現しました。
ダイセル社は2020年、生産現場で収集したデータを人工知能 (AI) が学習することで、「自律型生産システム」を開発し、「ダイセル式生産革新手法」を劇的に進化させました。
具体的には、更なる生産性向上を実現する「最適運転条件導入システム」(PCM)と、更なる生産の安定化を実現する「高度予知予測システム」(APS)です。
「最適運転条件導入システム」(PCM)は、AI技術の進化により、約20年前のダイセル式生産革新ではシステム化出来なかった最適運転が可能になりました。
「高度予知予測システム」(APS)は、安全・品質・生産量・コストの悪化につながるプロセス・設備の変調を予測し、最適運転が可能になりました。
同社は「自律型生産システム」により、人とシステムの役割分担を整理するなど、工場の働き方改革をおこない工場運営の全体最適化を推し進め、その結果、グループ全体で年間最大100億円のコスト削減が見込まれます。
経済産業省が2018年に定義したDX(デジタル・トランスフォーメーション)は、製品、サービス、ビジネスモデルだけでなく、業務、組織、プロセス、企業文化・風土という「企業組織・企業活動」も変革し、他の会社よりも儲かる仕組みをつくることと言えます。
ダイセル社は、20年前からDXで生産革新を実現しました。PCM、APSの2つのシステムは今後、グループ企業やサプライチェーンに拡大し、サプライチェーン全体でのエネルギーの最適化を図るとしています。
次回統合報告書ではグループ企業、サプライチェーンでの成果を情報開示されてはいかがでしょうか。